We support our Publishers and Content Creators. You can view this story on their website by CLICKING HERE.
Key Points: Huntington Ingalls Industries (HII) has identified welding issues on U.S. Navy warships and submarines, impacting over two dozen vessels, including three in active service.
-An internal investigation revealed that fewer than two dozen welders skipped preheating steps necessary for critical welds.
-HII and the Navy are assessing the affected welds to determine necessary repairs, potentially affecting timelines for the completion of Virginia-class submarines and Gerald R. Ford-class carriers.
-Meanwhile, the U.S. shipbuilding industry faces labor shortages, prompting discussions on workforce training and retention.
-Robotic welders, like Fincantieri’s MR4Weld, may provide a long-term solution by ensuring precise and consistent welding processes.
U.S. Shipbuilder Addressing Welding Issues for U.S. Navy
One of the largest shipbuilders in the United States has completed an internal investigation into how faulty welds were present on United States Navy warships and submarines. Earlier this fall the Navy notified lawmakers that more than two dozen vessels – including three currently in service – received faulty welds at Huntington Ingalls Industries Newport News Shipbuilding (NNS).
In late October, HII claimed that fewer than two dozen shipyard workers were found to be responsible for the faulty welds on the U.S. Navy’s Gerald R. Ford-class nuclear-powered aircraft carriers and Virginia-class fast attack submarines now under construction.
The company said at the time that based on its initial investigation, there was no indication that it was the result of malicious intent. This week, Jennifer Boykin, NNS president and HII executive vice-president told international military analyst firm Janes that the welders were part of a force of 1,700 workers at the facility and they “skipped a step” in the welding process. It was later identified via self-reporting or other shipyard reporting.
“All welds are different,” Boykin said during an interview conducted in advance of the christening of the future Virginia-class fast-attack submarine USS Arkansas (SSN-800) on Saturday. “Welds have low, medium, and high criticality. For some welds, depending on the requirement, you preheat the metal to get to a certain temperature.”
The preheating step was reportedly “skipped,” resulting in the faulty welds.
“The metal wasn’t heated as long [as required] or not heated,” Boykin added.
US Navy Virginia-class Submarine Under Construction.
As a result, HII and the U.S. Navy have introduced a method to test and assess the welds, which will determine whether a repair is necessary.
“I’m sure there will have to be some work,” said Boykin, but didn’t indicate how long the process could take to be completed, or if it would disrupt the timeline for the completion of future warships. The U.S. Navy is already facing significant delays in receiving its Virginia-class boats.
Problems Are Deeper Than Faulty Welds
The other unanswered question is what will happen to the dozen or so welders who skipped a seemingly crucial step. In other industries, it is possible the workers could be terminated for cause, but that could only add to the problems – as the U.S. shipbuilding industry faces an ongoing challenge to attract, train, and retain skilled workers.
The entire U.S. maritime industrial base has faced a serious labor shortage, as there aren’t enough new workers to replace those who are retiring. In June, the U.S. Navy established a “Direct Reporting Program Manager” for the Maritime Industrial Base (DRPM-MIB), who could help oversee investments needed to restore shipbuilding capacity.
The U.S. Navy also announced in September that it was seeking to work with private industry to grow its submarine industrial base, which has shrunk to one-third of its capacity from 30 years ago.
Robot Welders to the Rescue?
However, the solution to the problem may already be here – robot welders!
Just as the U.S. Navy is looking at autonomous platforms to serve as a force multiplier for its warships, it will likely see those vessels built – at least partially – by robots. In July, shipbuilder Fincantieri, which is employing robots to aid in the building of the U.S. Navy’s new Constellation-class frigates, unveiled its MR4Weld (Mobile Robot for Welding).
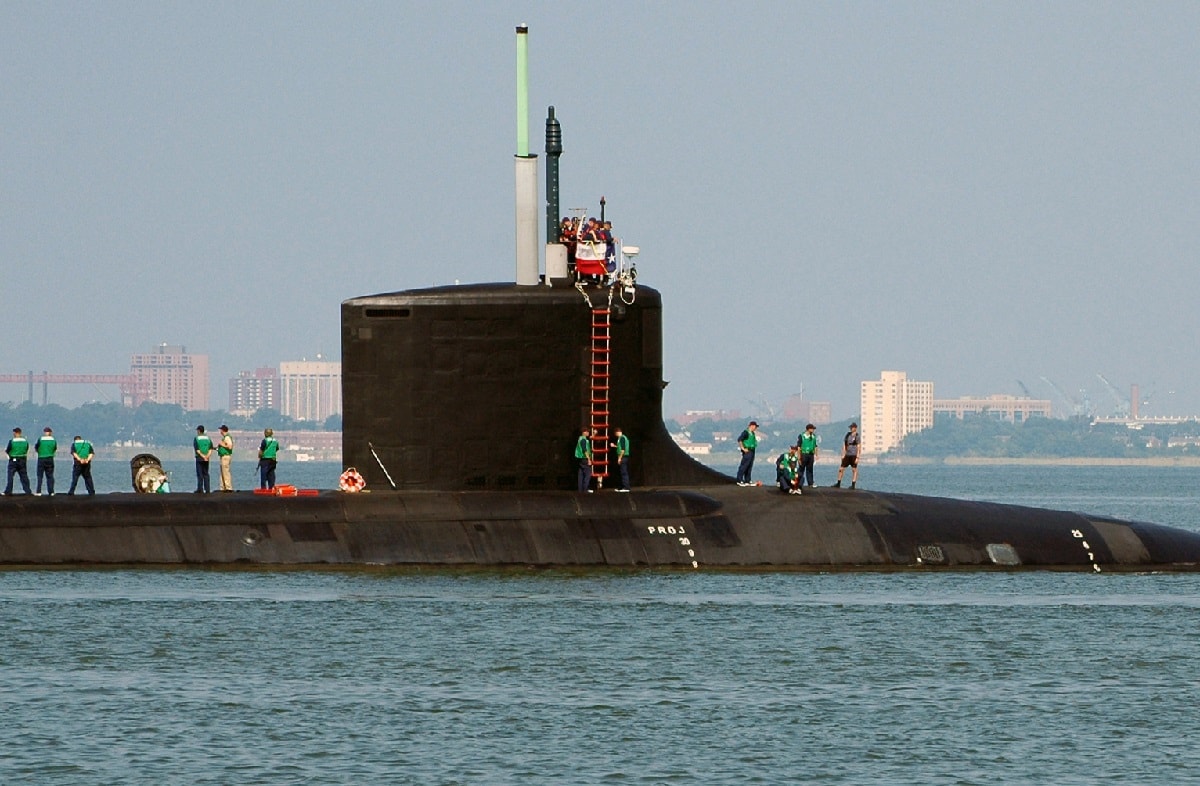
U.S. Navy Sailors stationed aboard the Virginia Class New Attack Submarine Pre-Commissioning Unit (PCU) TEXAS (SSN 775) stands topside as the boat gets underway from Naval Station Norfolk, Va., Aug. 22, 2006. TEXAS is the second Virginia Class submarine built and the first major U.S. Navy combatant vessel class designed with the post-Cold War security environment in mind. TEXAS will be commissioned Sept 9, 2006 in Galveston, Texas. (U.S. Navy photo by Mass Communication Specialist Seaman Kelvin Edwards) (Released)
The tracked welding robot was co-developed with Italian firm Comau, which created a platform that is already active in the automotive industry.
MR4Weld is built around a high-payload, 6-axis articulated robot fitted with a welding torch that is installed on a tracked undercarriage and equipped with an integrated vision system to autonomously identify welding joints. It can employ digital tools to collect welding and production data, which is used to record welded joints. Once programmed, the robots will never skip a crucial step.
Author Experience and Expertise: Peter Suciu
Peter Suciu is a Senior Editor focusing on defense issues for 19FortyFive. He has contributed to more than four dozen magazines, newspapers, and websites with over 3,500 published pieces over a twenty-year career in journalism. He regularly writes about military hardware, firearms history, cybersecurity, politics, and international affairs. Peter is also a Contributing Writer for Forbes and Clearance Jobs. You can follow him on X: @PeterSuciu – and on Bluesky: @petersuciu.bsky.social.